Professional Welding Inspection Services in Gilbert Arizona: What You Need to Know
Professional Welding Inspection Services in Gilbert Arizona: What You Need to Know
Blog Article
Exploring the Importance of Welding Inspection in Industrial Applications: Safeguarding Versus Failures and Enhancing Long Life
Welding evaluation works as an essential line of protection in industrial applications, guaranteeing the structural honesty and integrity of bonded parts. By methodically identifying problems such as porosity and insufficient combination, inspections not just prevent failures but likewise prolong the lifespan of necessary assets. Abiding by industry requirements improves both safety and security and functional efficiency; nevertheless, the implications of overlooking these practices can be severe. As we examine the diverse benefits of routine inspections, it comes to be evident that recognizing these dynamics is not merely an issue of compliance but a strategic critical for durability and threat mitigation (Welding Inspection Gilbert Arizona).
Function of Welding Inspection
Welding assessment acts as a critical safeguard in industrial applications, making sure that bonded structures satisfy specified criteria of top quality and safety. This process includes a methodical evaluation of welds to validate their integrity, strength, and conformity with well-known codes and specs. The role of welding evaluation is complex, including both visual assessments and non-destructive screening approaches, which might consist of ultrasonic, radiographic, or magnetic fragment screening.

In addition, welding evaluation plays an important role in governing conformity. Numerous sectors are controlled by rigid security criteria, demanding comprehensive paperwork and validation of welding methods. By keeping these documents, companies can demonstrate adherence to safety regulations, consequently cultivating depend on amongst stakeholders and clients. Eventually, the role of welding evaluation is indispensable in promoting safety, enhancing performance, and protecting investments in commercial infrastructure.
Usual Welding Flaws
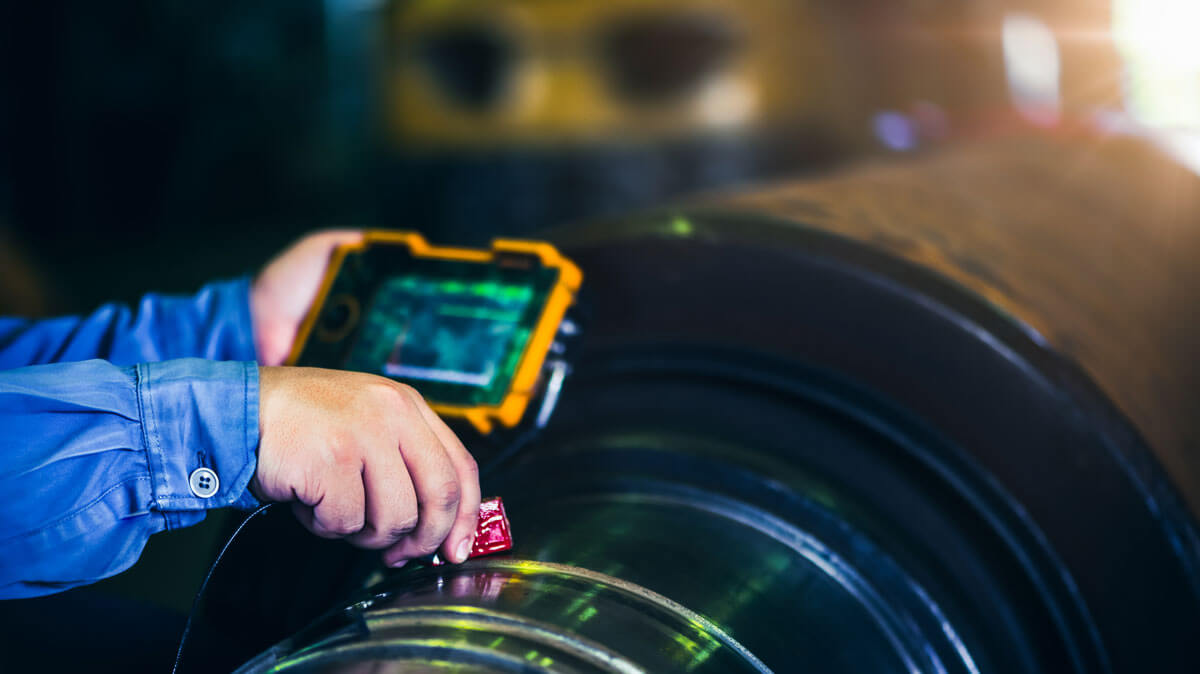
One of one of the most common issues is porosity, defined by tiny gas pockets caught within the weld metal. This happens because of contaminants or inappropriate shielding gas, jeopardizing the weld's stamina. Another significant problem is incomplete fusion, where the weld metal fails to bond correctly with the base product, potentially causing architectural weaknesses.
Cracks can additionally develop during or after the welding process, usually associated to thermal stress and anxieties or incorrect air conditioning rates. Additionally, damaging, where the base steel is worn down along the weld grain, can compromise the joint and is typically triggered by too much heat input or incorrect strategy.
Moreover, absence of infiltration takes place when the weld metal does not reach the origin of the joint, leading to poor strength. Comprehending these usual problems is important for welders and inspectors alike to ensure that welded frameworks meet safety and security and performance criteria, inevitably protecting against potential failings in industrial applications.
Benefits of Routine Assessments
Routine evaluations function as an essential protect in ensuring the integrity and longevity of bonded structures. These analyses determine possible problems and weak points that may jeopardize the integrity of welds, enabling prompt removal prior to problems intensify. By implementing a structured assessment routine, organizations can considerably decrease the risk of tragic failings that might cause costly downtime, tools replacement, and even accidents.
Moreover, routine examinations add to boosted quality assurance throughout the welding process. By sticking to a constant assessment schedule, business can make certain that their welding practices meet recognized high quality criteria and ideal practices. This not just cultivates a society of liability yet additionally urges constant improvement among welding personnel.
On top of that, normal evaluations his comment is here help with much better maintenance planning. By identifying wear and tear early, organizations can strategically arrange replacements and repair services, minimizing interruption to operations. This positive method ultimately leads to prolonged asset lifespan and enhanced overall productivity.
Lastly, a dedication to regular assessments can enhance a firm's reputation in the industry. Customers and stakeholders significantly value companies that focus on security and high quality, thereby boosting trust fund and possibly bring about increased service opportunities.
Sector Requirements and Regulations
Abiding by market requirements and regulations is a fundamental element of welding evaluation that complements the advantages of normal evaluations. These criteria, developed by companies such as the American Welding Culture (AWS) and the American Society of Mechanical Engineers (ASME), give a framework for finest practices in welding processes, products, and assessment techniques. Conformity with these guidelines guarantees that welds fulfill the needed quality and safety standards, substantially minimizing the threat of structural failings.
Regulative bodies like the Occupational Safety And Security and Health And Wellness Management (OSHA) better enforce standards that secure workers and the atmosphere throughout welding procedures. By adhering to these developed criteria, markets can boost the reliability of their components and structures, ensuring they execute as planned under various operational problems.
Additionally, adherence to sector criteria fosters consistency in quality assurance, facilitating smoother interaction among stakeholders and regulatory agencies. This placement not only lessens liability risks yet likewise boosts the reliability of organizations in competitive markets. Ultimately, conformity with welding standards and laws is not simply a legal obligation; it is an important financial investment in safety, performance, and long-term functional success.
Future Trends in Welding Evaluation
As markets remain to develop, the future of welding evaluation is poised to integrate innovative innovations that enhance accuracy and performance. Among the most considerable fads is the adoption of automation and robotics in examination procedures. Automated systems can perform evaluations swiftly, decreasing human mistake and boosting throughput in manufacturing atmospheres.
In addition, the assimilation of expert system (AI) and artificial intelligence formulas will allow anticipating analytics, enabling real-time evaluations and proactive upkeep (Welding Inspection Gilbert Arizona). By analyzing click here for more information from previous examinations, these innovations can identify patterns that might suggest prospective failings, therefore prolonging the life expectancy of welded parts
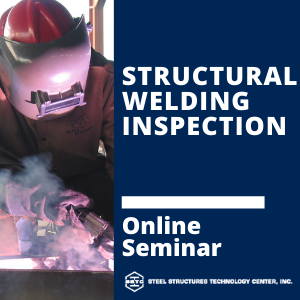
Moreover, the trend towards digitalization will certainly bring about enhanced information monitoring systems that assist in far better tracking, reporting, and conformity with market standards. In summary, the future of welding evaluation is identified by technical developments that assure to significantly improve integrity, safety, and functional efficiency in different commercial applications.
Conclusion
Finally, welding evaluation offers a crucial function in ensuring the integrity and longevity of welded structures throughout numerous industrial applications. By recognizing problems such as porosity and insufficient fusion, regular examinations play a considerable role in threat mitigation and quality guarantee. Adherence to market requirements and guidelines further boosts functional safety and reliability. As advancements in innovation remain to progress, the future of welding evaluation assures raised precision and effectiveness, inevitably adding to the longevity of essential facilities.
Welding assessment serves as an essential line of protection in industrial applications, ensuring the structural integrity and integrity of bonded elements.Welding examination serves as a crucial safeguard in commercial applications, ensuring that welded structures satisfy specified criteria of high quality and safety and security - Welding Inspection Gilbert Arizona. Inevitably, the function of welding evaluation is essential in advertising security, enhancing performance, and click to investigate securing investments in commercial framework
These criteria, established by organizations such as the American Welding Society (AWS) and the American Society of Mechanical Designers (ASME), supply a structure for finest techniques in welding procedures, materials, and assessment methods.In conclusion, welding inspection serves a crucial function in making certain the stability and toughness of welded structures across various industrial applications.
Report this page